Once upon a time in the gold valley off the Italian roads of Valenza, a jewelry pioneer recently acquired by the legendary LVMH group decided to plunge into the project of a lifetime. Bvlgari just unveiled the largest and 100% sustainable jewelry manufacture in Europe. A manufacture built on modernity, sustainability and jewelry anchored in the oldest golden city.
Largest manufacture in Europe
Passing through Italian villages as if we were traveling through a Fellini movie from sixties… it comes to quite a shock or vivid reality when the car parks in front a gigantic modern building next to a glass cube and a small house with Venetian blinds. A perfect bridge between innovation and tradition. Under the guidance of renowned architect Peter Marino, the Bvlgari Manufacture opened its doors mid-March after an 18-month construction project to build a 15’000 square feet facility. A prowess. It resulted into the largest European manufacture ever built respecting the environment.
Jean-Christophe Babin, CEO of the Bvlgari Group, explained that “With this project, Bvlgari is betting on the worth of its roots and expertise that has been handed down over the centuries. The art of goldsmithing is an area in which Italy particularly excels in. »
When it all started: Gold & Valenza
Why there? Why now? One hundred and seventy years ago, not only Francesco Caramoso was the first goldsmith to register his work in Valenza but he also happened to be the very first man who moved in the city of gold. At a very young age his uncle taught him to become a goldsmith. When he got married, Caramoso set up his own business named Cascina dell’Orefice -the Villa Clerici a historical building in which the very first goldsmith workshop was ever built- and started teaching people around him. A slow but sure process that transformed Valenza into what it is today: the most famous city of gold.
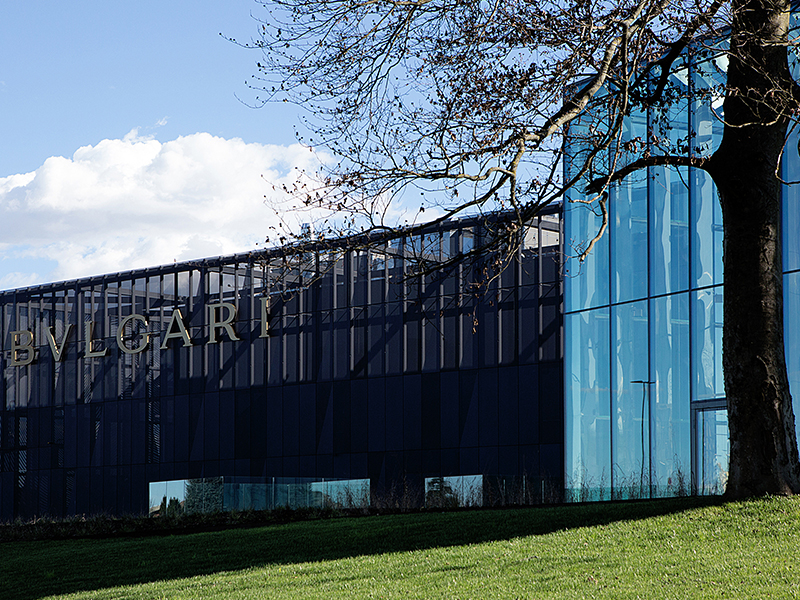
« We have traces of this building when Caramoso moved here, » explains Raffaella Di Vita, Bvlgari manager for the International Press Relations. « The glass house happens to be at the exact position where Caramoso used to work… no wonder why Bvlgari decided to go on with a new adventure right there. Right now. »
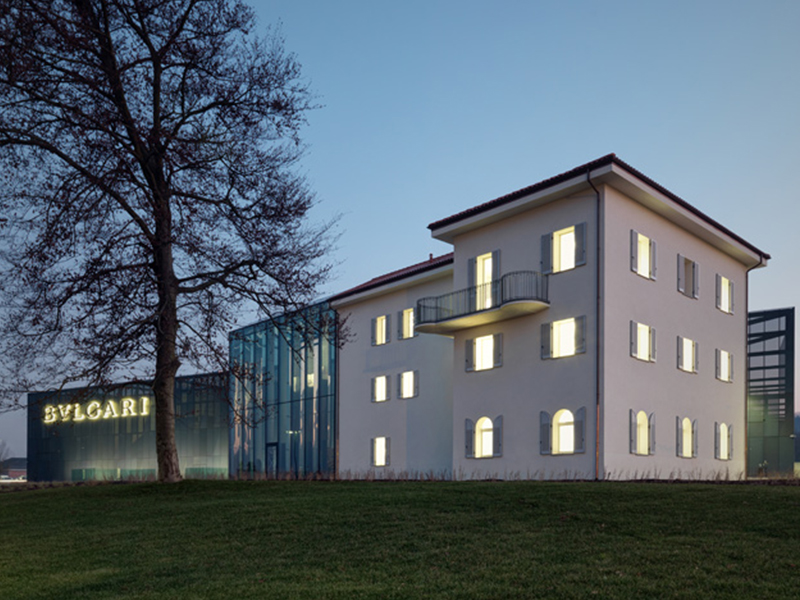
Sustainability to its paroxysm
Towards the end of the year, the manufacture expects to win the LEED international certification (Leadership in Energy & Environmental Design). While committing to corporate social responsibility (CSR), the CSR programs operate in conjunction with the LVMH group’s sustainability programs such as LIFE: LVMH Initiatives for the Environment. Being 100% sustainable, the building marks a huge commitment from the company to the country because Bvlgari will hire within the upcoming two and half years 300 people. As a matter of fact, the building was designed to integrate technologies that had the lowest environmental impact. For starters, the Bvlgari manufacture set-up a sustainable mobility offering alternatives to driving to reduce pollution such as shuttle busses and local transport hubs in addition to car-pooling. More than a third of the employees are already taking advantage of the system. When it comes to water efficiency, a plan was developed to reduce water usage and irrigation, reduce waste water and control the water supply inside the building. Last but not least: the energy. The glass « cube » building enables a maximum of natural light coming inside combined to LED lighting inside the production facilities. Speaking of which…
Islands of production
The Manifattura as they call it is divided in eighteen workshops baptized islands. It enables an efficient and centralized production on grouped product family. Each island has twenty-one high-skilled craftsmen divided into goldsmiths, stone-setters and polishers who receive kits of semi-finished products to work on in order to deliver finished products, controlled and ready to be shipped. Although the workforce is assisted with the latest machinery all controlled by tablet, it can never replace the hand of the man. Therefore, 21 craftsmen per island stretch the gold, polish and stone-set each piece of jewelry by hand on a daily basis since January 9th of this year.
The added value? Nicolo Rapone, who is the Jewelry Business Unit Operations Director at the Bvlgari Manufacture only has one word for it : perfection. He explains that by centralizing all the skills within a same area, despite the assigned work task, it drastically increases the team building efficiency. The collaboration between human-beings marks the difference. « The most complex thing is to do something well-made to perfection and together, otherwise you have to do it all again. »
The way it works? It goes without saying that if the Italian brand has made their name a legend in the industry and national culture is by the degree of creativity and level of craftsmanship. Each and every piece is made internally integrating the various stages of jewelry production including 3D and lost wax casting technique where a motif is made on a wax pattern from a 3D then invested into a mold with plaster. From B.Zero1 to Serpenti each collection motif follows the same production technique. What they don’t master, they outsource like the chains for example.
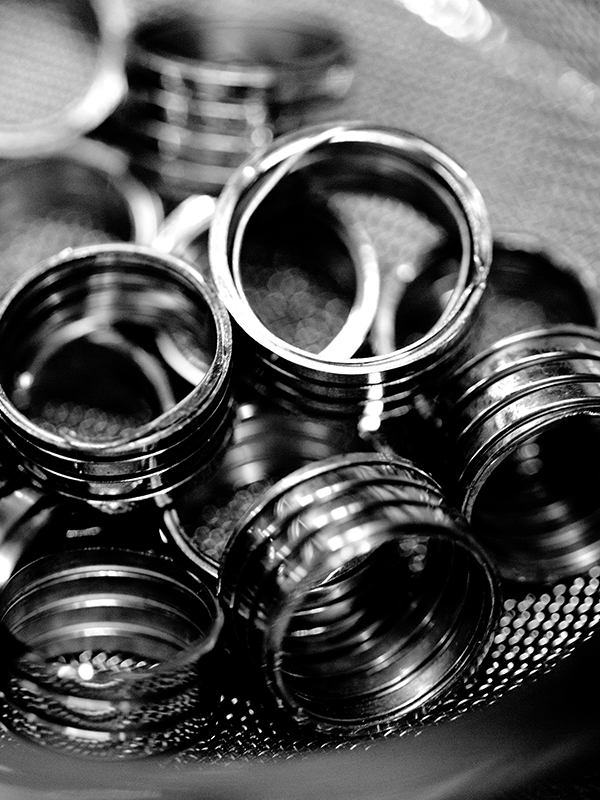
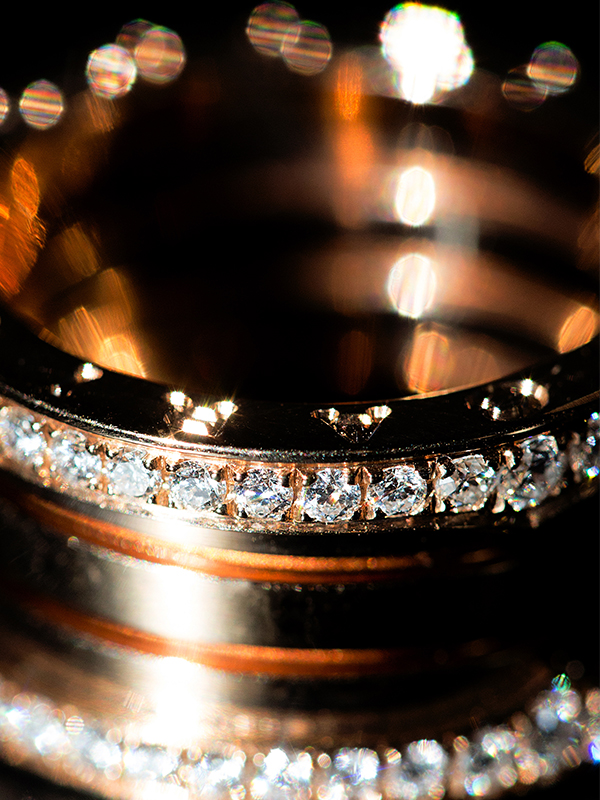
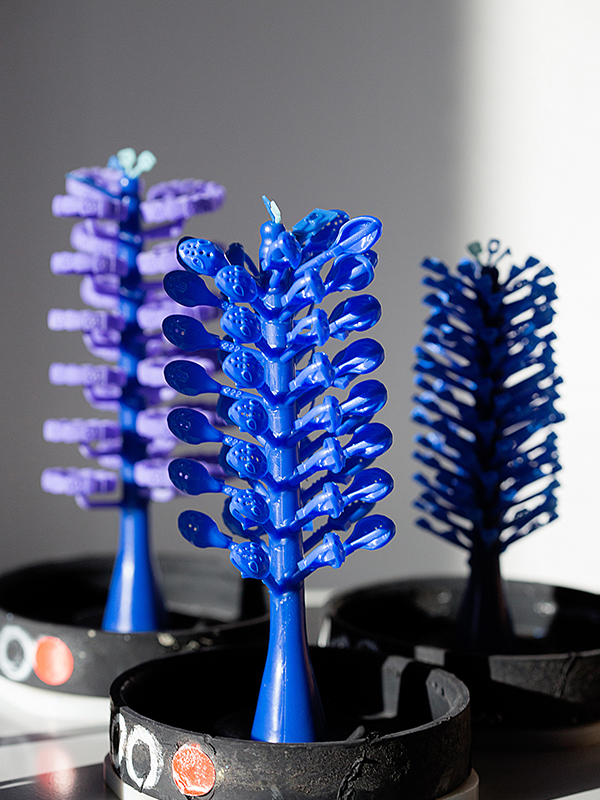
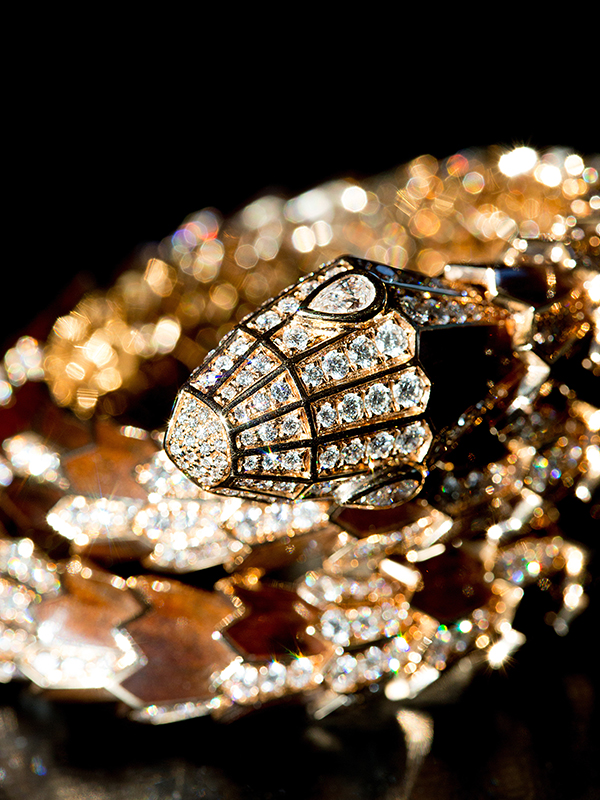
The Bvlgari Jewellry academy
Walking around the Manifattura is like walking in a giant haze surrounded by large glass windows filled with daylight and passing by workers in marine blue uniforms until we suddenly enter a corridor with a large tree painted on the wall with colored branches and leaves as if we entered the playground of a school. Close but not quite. The playground is the new Bvlgari Jewellery Academy and the kids are the first forty privileged students who managed to enter the program.
Rapone explains, « The goal of the Bvlgari Academy training is to create the very best crafmanship in Italian manufacturing. Considering that the « Made in Italy » remains a guaranty for everyone in jewelry. Bvlgari wants to leave an imprint with the manufacture and its new academy forming and creating new people. » Jewelry and goldsmithery schools are everywhere in Italy and most specifically in the regions of Valenza, Vicenza and Ariso forming artisans to the jewelry craftmanship. Bvlgari will hire the best students of these schools, up to 300 people in the next two and half years. « People coming to the academy are already professionals and each student is hired by Bvlgari when they enter the training program that lasts approximately four to six months, » add Rapone. A degree from the Bvlgari Jewellery Academy only complements an existing diploma but who knows, it may eventually become the ultimate specialization in the industry!
Bvlgari – Master of certification
Being fully responsible and concerned about the environment, needless to mention that each and every Bvlgari piece of jewelry possesses two certificate including the Responsible Jewelry Council and the Code of Practice following the Kimberly process in using conflict-free diamonds. To push it even further, Bvlgari is the first brand who obtained the certification of chain custody for the use of metal, as a matter of fact: gold. It means that they officially demonstrate that what they buy is traced back into their production chain proving that the gold comes from a country that does not finance illegal actions.
The opening of the Italian Manufacture in Valenza sets a new milestone in the history of the LVMH group and expansion of Bvlgari. By keeping the production of the one-of-a-kind piece in their home, Roma and their watch production in Neuchatel, Switzerland –Bvlgari increases it capacity of producing exclusively their iconic B.Zero1, Serpenti, Diva and Parentesi collections following their quality standards and environmental implications. Also, they will keep on outsourcing suppliers within the golden city to keep on offering a large selection of dazzling creations made with the right sets of mind.
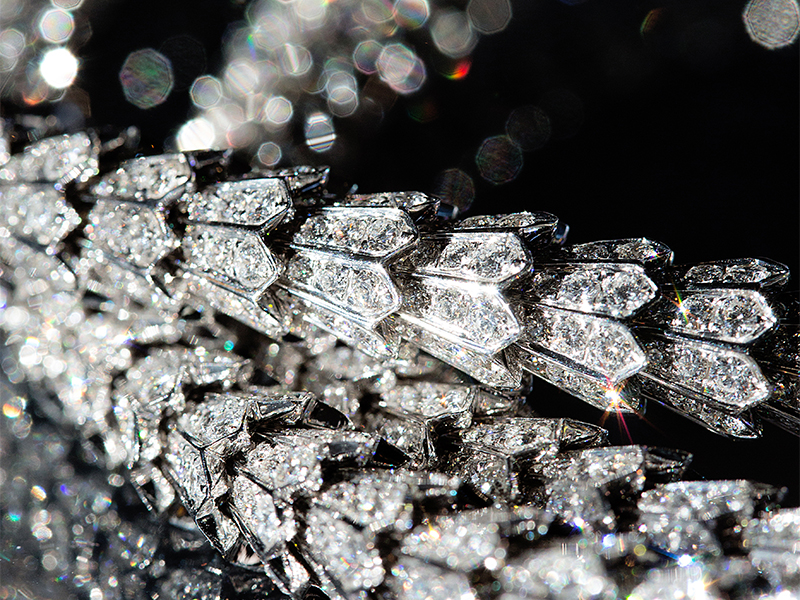